The construction industry is an important customer for Metsä Fibre’s sawn timber, both in Finland and in export markets. The products are used for diverse purposes, some of the most common being apartment buildings and infrastructure sites, where Metsä Fibre’s planks and boards are used from the piling stage onwards.
“Sawn timber is still a raw material without parallel for scaffolding and cast moulds on construction sites. It offers a good weight-to-strength ratio. Sawn timber is also light and easy to process, which makes it easier to handle on construction sites,” says Ville Valio, Area Sales Director for Europe at Metsä Fibre.
To cite another example of the diversity and adaptability of sawn timber, boards and planks can also be used in massive cast moulds for highway ramps and bridges. The recyclability of sawn timber is an added bonus that is increasingly appreciated.
“Our trump cards are consistent quality as well as large volumes, reliable deliveries and efficient logistics,” says Valio.
Demand for sawn timber grows in export markets
Most of the output of Finland’s largest sawn timber producer goes for export, where the company tries to transport sawn timber and pulp together. Ideally, customers can track their deliveries in real time.
Tommi Saarnisto, Area Sales Director for the Americas, Middle East and North Africa, points out that sawn timber is becoming increasingly in popular on construction sites in North Africa and the Middle East.
There is a shortage of trees in both regions, and boards and planks have not been replaced by building board, as they have in Europe.
“Sawn timber is a much more convenient option. It is also easier to cut to size,” says Saarnisto.
Metsä Fibre is a trusted partner for log house manufacturers
After a slower period, the market for log houses and wood construction overall are seeing positive development, both in Finland and abroad. The coronavirus pandemic has boosted interest in summer cottages, and logs are gradually also finding their way into public buildings, like schools and daycare centres.
Metsä Fibre’s customer base includes several Finnish log house manufacturers, which the company supplies with high-quality sawn timber products for laminated logs. In product development Metsä Fibre cooperates closely with the manufacturers.
Ville Valio says that matters of raw materials, consistent product quality and reliable deliveries are especially important in these customer relationships.
“Modern laminated log is made by gluing several layers together. A wall consists of many such logs stacked one on top of another, so they need to look as uniform as possible. This calls for consistent quality in production, but also requires raw material of a very high quality, since pine growth differs widely in different parts of Finland.”
The wood most suitable for each customer’s needs is selected well in advance – in practice, where it grows. In addition, sawmills have been fitted with 3D and X-ray equipment for logs. Drying methods have also been developed to meet the most stringent demands and quality requirements.
“Many of our log house industry customers consider Nordic wood to be the best,” says Ville Valio.
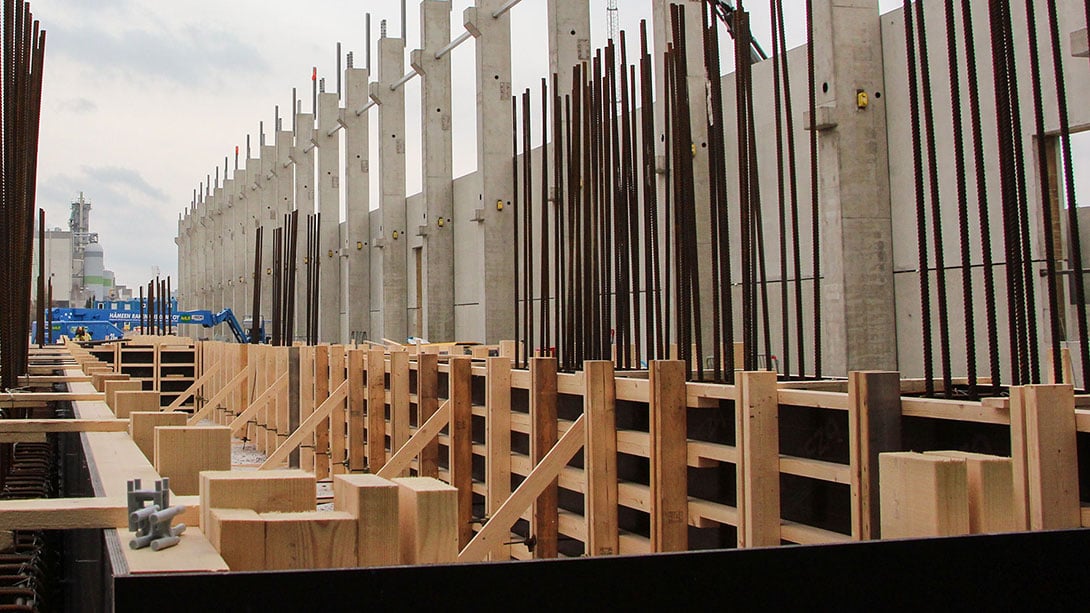
Raw material for glulam shipped to export markets
Among Metsä Fibre’s main sawn timber customers are manufacturers of glulam beams. Like log house manufacturers, they also have exacting quality criteria.
Glulam beams are used in the frameworks of new buildings and must therefore satisfy the requirements for consistent quality and uniformity, as well as those related to the strength and long lifecycle of wood, and the technical quality of products.
Most of the output goes to construction sites of single-family houses in Japan, where earthquakes are common. A major construction site will soon be launched in Finland, too. The roof structures of the pulp warehouse at the new bioproduct mill in Kemi will be made of glulam beams. This site alone calls for more than 50 full trailers of sawn timber.