The dried pulp produced on the new bioproduct mill’s pulp line is cut and baled into either two-tonne export units or one-tonne units for domestic use.
The baling plant’s automated system makes a load of the units, which is moved to the loading table. In addition to automation, only the driver’s input is required to load the products from the table into the vehicle.
“In cooperation with Kuljetusliike Kalevi Huhtala, a transport company, we have developed a transport fleet and adapted it to mill traffic. The driver switches the power on in the trailer, as well as the conveyor’s control logic, and then starts up the automated loading function, which transfers the bales from the loading table onto the vehicle in two to three minutes. It used to take forklift trucks just as long to perform one or two lifts,” says Pasi Pulkkinen, VP Logistics at Metsä Group.
The mill uses four identical 23-metre semi-trailers that have special permission to exceed the maximum permissible weight specified in the road traffic act.
“What makes this unique is that we have a special fleet that can carry 66–72 tonnes. This allows us to reduce the number of visits to the mill to around a third of that in the past, which is a considerable change.”
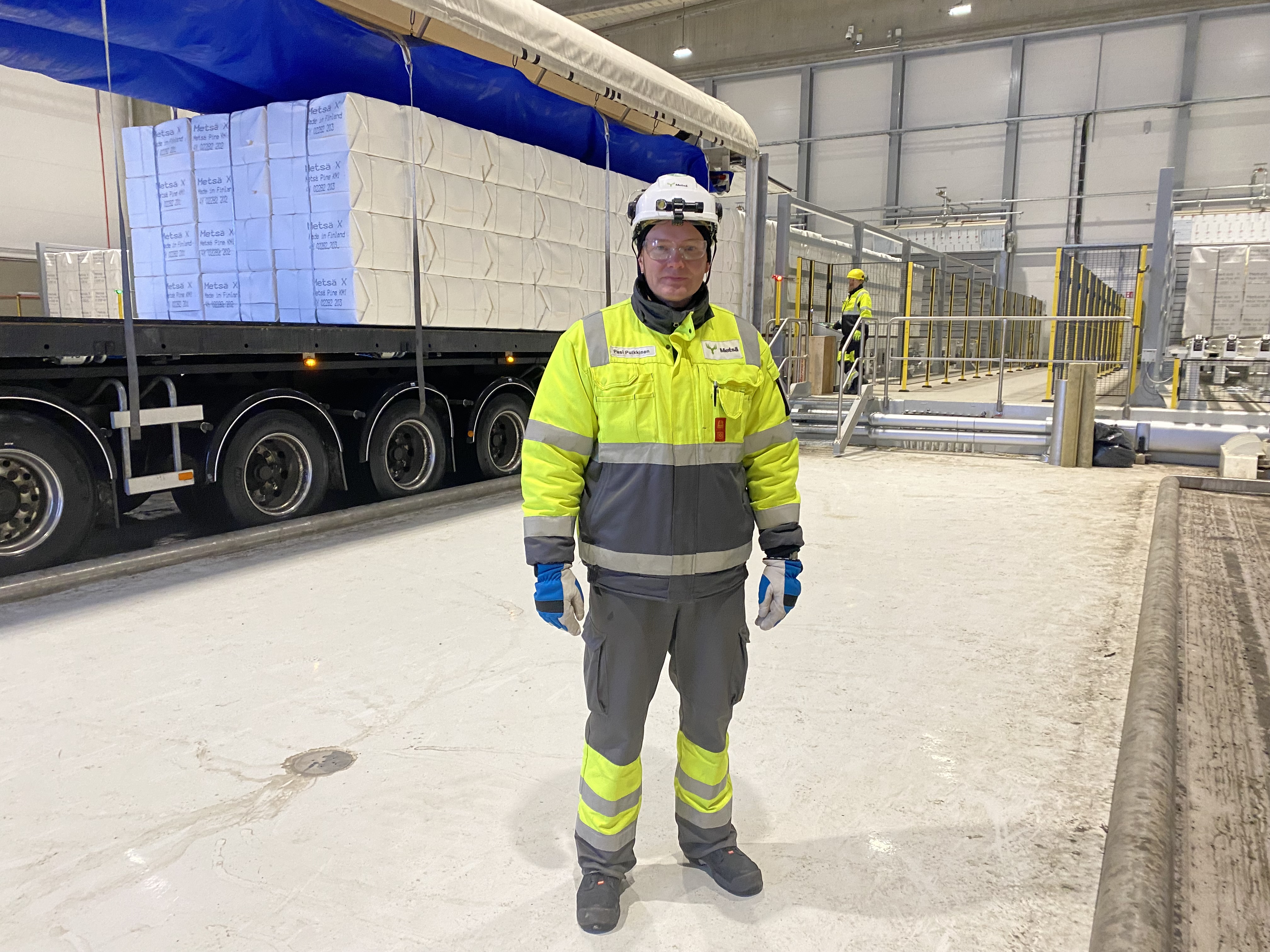
New product warehouse at the Port of Ajos
Once the mill reaches its planned production capacity, 50–60 transports will leave daily from the bioproduct mill to the Port of Ajos 15 kilometres away.
“The wooden product warehouse in Ajos features three unloading sites. The bales are unloaded with similar automated equipment used for loading at the bioproduct mill. The unloaded products are then arranged on the unloading table into ready lifting units for the port’s electric forklift trucks,” says Pulkkinen.
The Kemi bioproduct mill produces 1.5 million tonnes of softwood and hardwood pulp annually. This is 2.5 times more than at the old mill.
Transport operations have been organised systematically across the integrated mill, as transports are integrated with Metsä Board’s neighbouring paperboard mill. Paperboard transports are handled with similar equipment, enabling the comprehensive management of product traffic.
The first weeks operating the new heavy transport fleet have shown that the fleet is working exactly as planned, and the experiences have been positive.
“The fleet moves smoothly along the planned route, the driving distances and routes work as planned, and loading and unloading operations have started up well.
At the port, the pulp bales are loaded onto ships for transport to the main market areas – Asia, Europe and North America.
The bioproduct mill’s warehouse in Ajos covers 37,000 square metres.
“The idea is to have no warehouse at the mill but to run our product warehouse at the Port of Ajos instead. This makes operations more streamlined and efficient, and requires fewer resources,” says Pulkkinen.