The Kemi bioproduct mill’s production process begins at wood handling, which receives its wood raw material primarily by rail along the new private electric track. According to Tomi Seppä, VP of the bioproduct mill, the bioproduct mill’s wood feeder equipment represents advanced technology.
“The autonomous and AI-based equipment for the reception, storage and process feeding of wood material is a world first. The electrically powered equipment and the systematic placement of functions enable woodyard operations to be run on fossil free fuel,” says Seppä.
From wood handling the wood is fed to the debarking department, where the wood is debarked and chipped.
Landmarks visible from a far
Even from far away, two great woodyard cranes stand out next to the mill’s debarking plant building. These cranes are new landmarks in the Sahansaari area. The woodyard’s electric and autonomous cranes reached their full height in the autumn of 2022, and their commissioning, involving testing and test runs, began at the beginning of 2023. They were brought into production during the third quarter of 2023, when the new bioproduct mill was started-up.
The woodyard cranes supplied by Andritz are the first of their kind in the world, and they unload wood from trains and trucks fully autonomously with the aid of artificial intelligence and machine vision. The cranes are electric and powered by the bioproduct mill, which shows a surplus in energy self-sufficiency. The bioproduct mill produces 2.0 TWh of renewable electricity each year, and its electricity self-sufficiency rate is 250 per cent. Electric cranes are part of the new mill’s fossil-free strategy and support Metsä Group’s sustainability objectives for 2030.
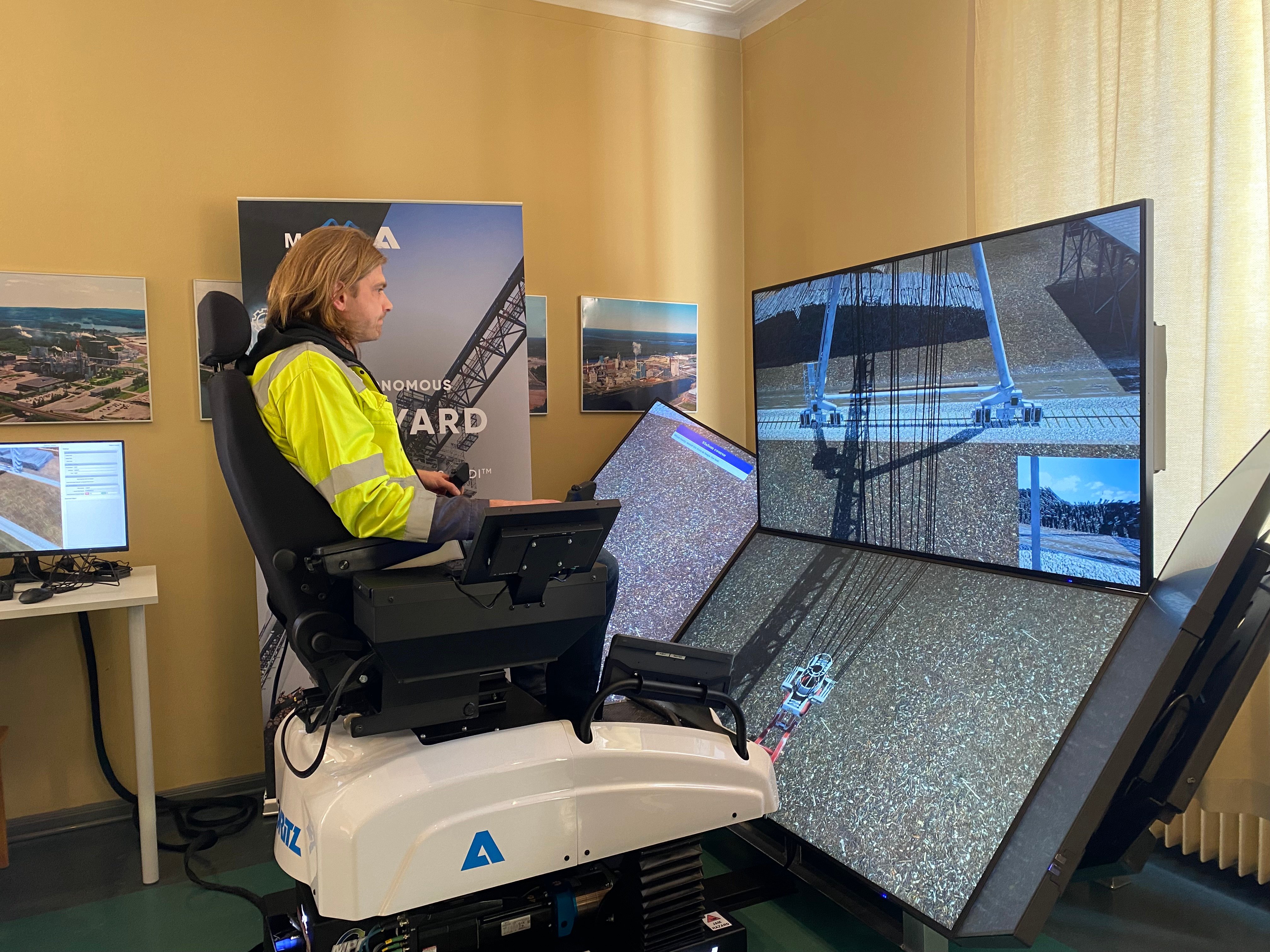
Training with a simulator
The new autonomous cranes are the first of their kind in the world, but their use has been practised for a while now. The crane simulator also supplied by Andritz has been used in operator training, and it has been well received by the trainees.
Before, diesel-powered telehandlers transported wood loads at the Kemi pulp mill. Tomi Seppä says that the new woodyard cranes improve the environmental, material and energy efficiency of wood processing.
“The new cranes are a significant technological leap forward. Electric cranes reduce wood waste and work more quietly than the current telehandlers. With the new cranes, there will be fewer work machines on-site,” says Seppä.
The need to transfer wood raw material has been minimised by placing the wood unloading areas, the woodyard and the autonomous woodyard cranes close to each other. Timber trucks use a one-way route to avoid encounters between vehicles, and there are no crossings between road and rail traffic. The trucks’ one-way routes also reduce the need for reversing. The noise levels of wood processing have also been considered. The wood unloading equipment is electrical and quiet in operation. The noise shielding of the barking drum and chippers has been further improved with soundproofing. In addition, noise barriers and noise walls reduce the noise impact on residential areas.