"The harmonisation has helped our work immensely at Metsä's production units. When we're familiar with the common guidelines for mills, we can prepare better for our duties and follow the correct procedures," says Toni Mikola. He has worked at the Rauma mill for some twenty years, currently as the Development Manager of Delete, a company specialising in process cleaning.
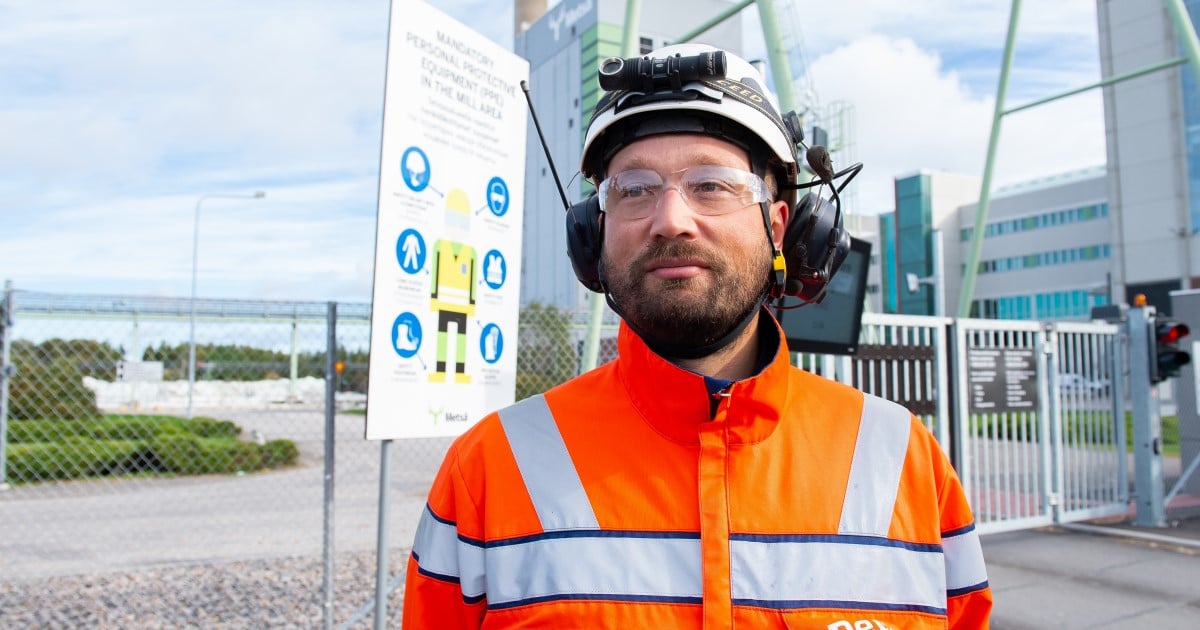
Delete's competence is needed to remove deposits from the lines or fix leaks in pipes, for example. According to Mikola, harmonised practices for protective equipment, lock-out/tag-out, and permits to work have proved extremely important. The permit to work procedure requires workers to plan in advance how to safely carry out their tasks.
"When we harmonised our permit to work procedure for high-risk tasks, we moved from oral to written permits. Now we know there's no room for interpretation. Planning the tasks and assessing the risks in advance also makes work more efficient."
According to Mikola, the changes have been welcomed positively and in a spirit of development at Delete.
"Continuous learning takes place at both Delete and Metsä, and we jointly discuss areas of improvement," says Toni Mikola.
Specific in Metsä's safety culture
In Toni Mikola's opinion, Metsä's safety culture supports dialogue and encourages development. There is one aspect where Metsä stands out– the culture of safety observations. "Metsä has a system and a set of objectives for them. The observations are discussed at morning meetings, and everyone can follow their development."
What elements make for a safe working environment?
"Safety comes from operating methods and attitude – both of which are needed. A good indicator of a safety culture is how often people turn a blind eye to defects. If there are no blind spots, the safety culture is in good shape", Mikola says.